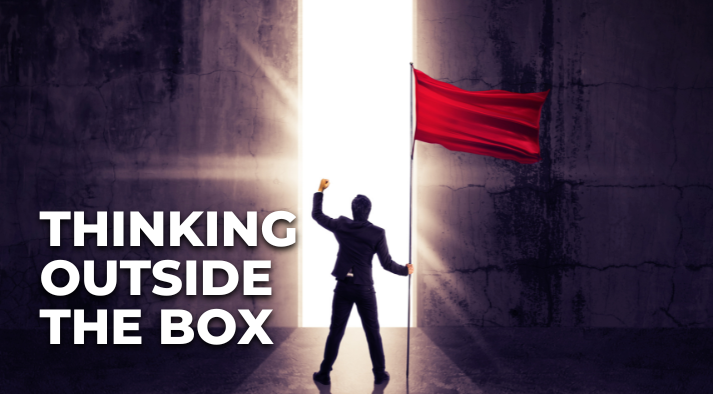
- August 28, 2025·
What are the insurance issues impacting those in the final mile? And how can carriers manage risk? “Thinking Outside the Box” recently interviewed Bryan Paulozzi, Vice President, Risk Strategies, part of the Brown & Brown team, to get his take on the industry today and tomorrow. Bryan and his team…